Surface Micro Machining: Key Concepts and Applications
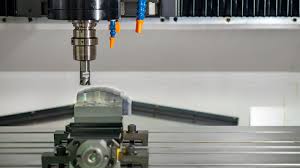
Surface micro machining refers to a process where extremely fine and precise features are created on the surface of materials, typically using advanced technologies like lasers, electrical discharge machining (EDM), or micro milling. These methods are crucial for creating intricate structures and patterns at the micro or nano scale, enabling the development of components for industries that require high precision and performance, such as electronics, medical devices, and automotive.
This article will explore the concept of surface micro machining its various techniques, applications, and how it is revolutionizing modern manufacturing.
What is Surface Micro Machining?
Surface micro machining is a precision manufacturing technique used to create very small, detailed features on the surface of a material. Unlike traditional machining processes that focus on removing large amounts of material, surface micro machining is primarily concerned with altering the top layer of a material to create micro-sized patterns or structures. These patterns can be as small as micrometers or even nanometers in size, and they are often used in microelectronics, sensors, and other high-precision applications.
This process typically requires advanced tools and machinery that can handle fine-scale operations and achieve high precision. The overall goal of surface micro machining is to produce functional, accurate features on the surface of materials while preserving the integrity of the underlying structure.
Key Techniques in Surface Micro Machining
There are several methods used in surface micro machining, each suited to different materials, designs, and production requirements. Below are some of the most commonly used techniques:
1. Laser Ablation
Laser ablation involves using a focused laser beam to remove material from the surface of a workpiece. The process can precisely etch and carve very fine features onto the material, making it ideal for surface micro machining. The laser’s high energy allows it to vaporize or melt the material in a controlled manner, creating clean, precise cuts.
Laser ablation is commonly used in the semiconductor and electronics industries, where it is used to produce microchips, integrated circuits, and other fine-scale components. Additionally, this technique is useful in creating microstructures on metal, ceramics, and polymers.
2. Electrical Discharge Machining (EDM)
Electrical discharge machining is a non-traditional machining process that uses electrical discharges to remove material from a workpiece. EDM is particularly effective for machining hard materials and creating intricate features with high precision.
In surface micro machining, EDM is used to create small holes, grooves, and other surface features. A series of electrical sparks between an electrode and the material surface erodes the material, resulting in highly accurate features. This method is often used in the production of molds, dies, and micro molds for the injection molding of small plastic components.
3. Micro Milling
Micro milling uses extremely small cutting tools to remove material from the surface of a workpiece. The process is similar to traditional milling but is specifically designed for fine-scale operations. Micro milling machines are capable of achieving high precision, with the ability to create features with dimensions as small as a few microns.
Micro milling is used in a variety of applications, including the fabrication of microfluidic devices, MEMS (Microelectromechanical Systems), and micro optics. The process allows for the production of intricate patterns and textures on metal, plastic, and composite materials.
4. Ultrasonic Machining
Ultrasonic machining involves the use of high-frequency sound waves to assist in material removal. The process uses ultrasonic vibrations to cause fine abrasive particles to abrade the surface of the material. This method is highly effective in creating micro features on brittle or hard materials like ceramics, glass, and hard metals.
Ultrasonic machining is especially useful for creating small holes, fine contours, and intricate surface patterns with high precision. It is often employed in the manufacturing of micro components for the aerospace, medical, and electronics industries.
5. Ion Beam Etching
Ion beam etching, also known as focused ion beam (FIB) machining, uses a beam of ions (typically gallium ions) to sputter material from the surface of a workpiece. The ions are accelerated and focused into a small beam, which is directed at the surface of the material. This process allows for the precise removal of material to create fine features at the micro or nano scale.
FIB machining is commonly used in semiconductor manufacturing and microelectronics for tasks such as circuit modification, defect repair, and micro structuring.
Applications of Surface Micro Machining
The precision and fine control of surface micro machining make it invaluable across various industries. Below are some of the key areas where surface micro machining plays a crucial role:
1. Microelectronics
Surface micro machining is a cornerstone of the microelectronics industry. The creation of microchips, semiconductors, and integrated circuits relies heavily on precise surface machining techniques. These components require extremely fine features to function effectively at the micro and nano scales, which is why surface micro machining is critical in their production.
Micro machining is used to create intricate patterns on the surface of silicon wafers, enabling the development of smaller, faster, and more efficient microchips. The process is also essential in producing the fine features on flexible electronics and wearable devices, which are increasingly in demand.
2. Medical Devices
Medical devices often require components that are not only highly precise but also biocompatible and durable. Surface micro machining is used to manufacture micro components for various medical devices, such as pacemakers, stents, and surgical tools. These components must adhere to strict standards of quality and precision.
For example, micro precision machining is used in the creation of microfluidic chips for lab-on-
Conclusion
Surface micro machining is a vital technology that enables the creation of highly precise, small-scale components for a wide range of industries. Through techniques like laser ablation, EDM, micro milling, and ultrasonic machining, manufacturers can produce intricate surface features that are essential in fields such as microelectronics, medical devices, aerospace, and automotive industries.
As technology continues to advance, the demand for surface micro machining will only grow. Its ability to enable miniaturization, improve performance, and create complex geometries at the micro and nano scales ensures that it will remain an essential process in modern manufacturing.